Động cơ xăng: một loại động cơ đốt trong tạo ra năng lượng bằng cách đốt cháy nhiên liệu lỏng dễ bay hơi (xăng hoặc hỗn hợp xăng, ví dụ như với ethanol) thông qua đánh lửa bằng tia lửa điện. Động cơ xăng có dải ứng dụng rộng, bao gồm ô tô, xe tải nhỏ, máy bay, tàu thuyền cỡ nhỏ, máy bơm, máy phát điện, máy công cụ và dụng cụ điện cầm tay. Động cơ xăng 4 kỳ được sử dụng phổ biến trong ô tô, xe tải nhẹ, xe máy cỡ trung bình đến lớn và máy cắt cỏ. Động cơ xăng 2 kỳ ít phổ biến hơn, thường dùng cho động cơ thuyền nhỏ và các dụng cụ làm vườn cầm tay (cưa xích, máy xén hàng rào, máy thổi lá).
Các loại Động cơ
Động cơ xăng có thể được phân loại dựa trên nhiều tiêu chí, bao gồm ứng dụng, phương pháp quản lý nhiên liệu, hệ thống đánh lửa, cách bố trí piston-xylanh hoặc rotor, số kỳ trong một chu trình, hệ thống làm mát, loại và vị trí van. Trong phần này, chúng được mô tả trong bối cảnh hai loại động cơ cơ bản: động cơ piston-xylanh và động cơ xoay.
- Động cơ piston-xylanh: Áp suất sinh ra từ quá trình đốt cháy xăng tạo ra lực tác động lên đầu piston, làm piston di chuyển tịnh tiến (qua lại) trong xylanh. Lực này đẩy piston ra khỏi đầu xylanh và thực hiện công.
- Động cơ xoay (Wankel): Không có xylanh và piston tịnh tiến thông thường. Thay vào đó, áp suất khí tác động lên các bề mặt của rotor, khiến rotor quay và thực hiện công.
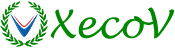
Động cơ Piston-Xylanh
Hầu hết các động cơ xăng là loại piston-xylanh tịnh tiến. Các thành phần thiết yếu của động cơ piston-xylanh được thể hiện trong hình. Hầu như tất cả các động cơ loại này đều tuân theo chu trình bốn kỳ hoặc chu trình hai kỳ.
Chu trình Bốn kỳ
Trong số các kỹ thuật khác nhau để thu hồi năng lượng từ quá trình đốt cháy, quan trọng nhất cho đến nay là chu trình bốn kỳ, một ý tưởng được phát triển lần đầu tiên vào cuối thế kỷ 19. Chu trình bốn kỳ được minh họa trong hình.
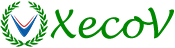
- Kỳ nạp: Với van nạp mở, piston đi xuống. Hỗn hợp hơi xăng và không khí dễ cháy được hút vào xylanh do chân không tạo ra.
- Kỳ nén: Piston đi lên, nén hỗn hợp, cả hai van đều đóng. Khi gần cuối kỳ, hỗn hợp được đốt cháy bằng tia lửa điện.
- Kỳ nổ (sinh công): Cả hai van vẫn đóng, áp suất khí do sự giãn nở của khí cháy tác dụng lên đỉnh piston.
- Kỳ xả: Piston đi lên đẩy khí thải ra ngoài qua van xả đang mở.
Sau đó, chu trình lặp lại. Mỗi chu trình cần bốn hành trình của piston (nạp, nén, nổ, xả) và hai vòng quay của trục khuỷu.
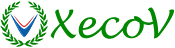
Nhược điểm của chu trình bốn kỳ là số kỳ nổ chỉ bằng một nửa so với chu trình hai kỳ (xem bên dưới) và công suất dự kiến chỉ bằng một nửa so với động cơ cùng kích thước ở cùng tốc độ hoạt động. Tuy nhiên, chu trình bốn kỳ giúp loại bỏ khí thải (quét khí) và nạp lại xylanh hiệu quả hơn, giảm thất thoát hỗn hợp nạp mới ra ống xả.
Chu trình Hai kỳ
Trong chu trình hai kỳ nguyên bản (phát triển năm 1878), kỳ nén và kỳ nổ (sinh công) của chu trình bốn kỳ được thực hiện mà không cần kỳ nạp và kỳ xả, do đó chỉ cần một vòng quay của trục khuỷu để hoàn thành chu trình.
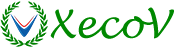
- Động cơ hai kỳ kiểu “uniflow” (dòng chảy đơn hướng): Hỗn hợp nhiên liệu mới được đưa vào xylanh qua các cổng chu vi nhờ một máy thổi khí (xem hình). Khí thải đi qua các van nấm (poppet valve) trong nắp xylanh, được đóng mở bằng cơ cấu cam-con đội. Các van được định thời để bắt đầu mở vào cuối kỳ nổ, sau khi áp suất xylanh đã giảm đáng kể. Các cổng nạp ở thành xylanh bắt đầu lộ ra sau khi việc mở van xả làm giảm áp suất xylanh xuống bằng áp suất nạp do máy thổi tạo ra. Các van xả vẫn mở trong vài độ quay của trục khuỷu sau khi các cổng nạp đã được piston đang lên che lại ở kỳ nén, do đó cho phép dòng chảy tiếp tục quét sạch xylanh kỹ hơn. Kỳ nén và kỳ nổ tương tự như của động cơ bốn kỳ.
- Phiên bản đơn giản hóa (1891): Sử dụng áp suất cacte để bơm hỗn hợp nạp mới vào xylanh. Thay vì các cổng nạp kéo dài hoàn toàn xung quanh thành dưới xylanh, động cơ này có các cổng nạp chỉ ở một nửa chu vi; một bộ cổng thứ hai bắt đầu cao hơn một chút ở thành xylanh ở nửa còn lại của đường kính xylanh. Các cổng lớn hơn này dẫn đến hệ thống xả. Các cổng nạp kết nối với một đường dẫn chuyển tiếp đến cacte kín hoàn toàn. Một van nạp có lò xo cho phép không khí vào cacte khi piston đi lên (kỳ nén). Không khí bị giữ lại trong cacte bị nén bởi piston đi xuống trong kỳ nổ. Do đó, piston làm lộ ra các cổng xả gần cuối kỳ nổ, và muộn hơn một chút, nó làm lộ ra cổng nạp, hoặc cổng chuyển, ở phía đối diện của xylanh để nạp hỗn hợp mới đã được nén từ cacte. Mặt trên của piston được thiết kế để tạo thành một bộ làm lệch hướng hoặc vách ngăn hướng dòng nạp mới lên trên ở phía nạp của xylanh và sau đó xuống dưới ở phía xả, do đó đẩy khí thải của chu trình trước ra ngoài qua cổng xả ở phía đó. Dòng chảy ra này tiếp tục sau khi các cổng nạp được piston đang lên che lại trong kỳ nén, cho đến khi các cổng xả được che lại và quá trình nén hỗn hợp nạp mới bắt đầu. Quá trình nạp này, được gọi là quét vòng (loop scavenging), là phương pháp đơn giản nhất được biết đến để thay thế khí thải bằng hỗn hợp mới và tạo ra một chu trình chỉ có kỳ nén và kỳ nổ.
Hệ thống như vậy được sử dụng trong nhiều động cơ xăng nhỏ (ví dụ: động cơ thuyền nhỏ) và cho các thiết bị chạy bằng xăng (ví dụ: máy phát điện di động). Nhiều máy hai kỳ nổi tiếng về tiếng ồn, khí thải carbon và các dạng ô nhiễm không khí khác mà chúng tạo ra, điều này đã khiến một số thành phố và tiểu bang của Hoa Kỳ cấm sử dụng một số thiết bị nhất định (ví dụ: máy thổi lá và động cơ thuyền hai kỳ). Một nhược điểm khác của động cơ hai kỳ là dòng khí hồi lưu gây ra một chút thất thoát hỗn hợp nạp mới qua các cổng xả. Do sự mất mát này, động cơ sử dụng bộ chế hòa khí hoạt động theo chu trình hai kỳ không tiết kiệm nhiên liệu bằng động cơ bốn kỳ. Có thể tránh được sự mất mát này bằng cách trang bị cho chúng hệ thống phun nhiên liệu (xem bên dưới) thay vì bộ chế hòa khí và phun nhiên liệu trực tiếp vào xylanh sau khi quét. Một sự sắp xếp như vậy là hấp dẫn như một phương tiện để đạt được công suất cao từ một động cơ tương đối nhỏ, và sự phát triển của bộ tăng áp (xem bên dưới Siêu nạp) cho ứng dụng này hứa hẹn sẽ cải thiện hơn nữa.
Động cơ Piston Đối đỉnh (Opposed-piston)
Động cơ piston đối đỉnh cũng cung cấp khả năng quét khí một chiều (uniflow scavenging). Động cơ này (xem phần A của hình) có hai piston di chuyển ngược chiều nhau trong cùng một xylanh. Hai bộ cổng kéo dài toàn bộ chu vi xylanh được bố trí sao cho một bộ được piston này đóng/mở và bộ còn lại được điều khiển bởi piston thứ hai. Trục khuỷu thứ hai, nơi các piston phía trên được gắn vào, nằm ở phía trên động cơ và hai trục được nối với nhau bằng bánh răng.
Thiết kế piston đối đỉnh có hai ưu điểm chính:
- Cân bằng tốt: Các khối lượng tịnh tiến di chuyển ngược chiều nhau, mang lại sự cân bằng tuyệt vời.
- Loại bỏ van: Loại bỏ các van nấm (poppet valve) cần thiết trong các động cơ hai kỳ quét khí một chiều khác.
Động cơ Xoay (Wankel)
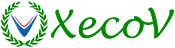
Khác hẳn với động cơ piston tịnh tiến quen thuộc, động cơ Wankel, phát minh bởi kỹ sư người Đức Felix Wankel, là một cuộc cách mạng trong thiết kế động cơ đốt trong. Thay vì piston di chuyển lên xuống trong xi-lanh, động cơ Wankel sử dụng một rotor hình tam giác cong, xoay tròn trong một buồng đốt có hình dáng đặc biệt, tựa như một hình oval dẹt.
Rotor này xoay quanh một trục lệch tâm, và ba đỉnh của nó luôn tiếp xúc với thành buồng đốt, tạo ra ba khoang kín có thể tích thay đổi liên tục. Chính sự thay đổi thể tích này thực hiện các quá trình nạp nhiên liệu, nén, đốt cháy và xả khí, tất cả diễn ra trong một vòng quay duy nhất của rotor.
Để điều khiển chuyển động phức tạp này, rotor được trang bị một bánh răng trong, ăn khớp với một bánh răng cố định nằm ở trung tâm buồng đốt. Trục đầu ra của động cơ, kết nối với rotor thông qua bộ lệch tâm, quay nhanh gấp ba lần so với rotor.
Hỗn hợp nhiên liệu và không khí được đưa vào buồng đốt qua cổng nạp, sau đó được đốt cháy bởi bugi. Khí thải sau đó được đẩy ra ngoài qua cổng xả. Việc làm mát và bôi trơn động cơ được thực hiện bằng dầu và nước tuần hoàn.
Điểm đặc biệt của động cơ Wankel là sự nhỏ gọn, trọng lượng nhẹ, vận hành êm ái và ít rung động. Tuy nhiên, việc đảm bảo độ kín cho các khoang đốt, kiểm soát tiêu hao nhiên liệu và khí thải là những thách thức kỹ thuật không nhỏ. Chính vì vậy, động cơ Wankel không được sử dụng rộng rãi như động cơ piston, nhưng vẫn có một vị trí đặc biệt trong lịch sử ngành ô tô, đặc biệt là với các mẫu xe thể thao của Mazda.
Cấu tạo và hoạt động cơ bản
Cấu trúc tổng thể của động cơ xăng phụ thuộc gần như hoàn toàn vào ứng dụng dự kiến. Ngoài loại chu trình (hai kỳ hoặc bốn kỳ), việc bố trí lắp đặt là sự khác biệt cấu trúc chính giữa động cơ ô tô, hàng hải, tĩnh tại và hàng không.
Khi sử dụng ly hợp và hộp số, như trong ô tô, động cơ thường thuộc loại “khối động lực thống nhất” (unit-power-plant) với vỏ hình chuông bao quanh bánh đà và được gắn vào mặt bích phía sau của khối xylanh, tích hợp hoặc gắn liền với vỏ hộp số. Ly hợp được tích hợp trong bánh đà của động cơ. Hệ thống treo ba điểm được sử dụng trong các động cơ như vậy; nghĩa là, các phần nhô ra ở mỗi bên của vỏ chuông khớp với các thành phần khung bên của xe, và một phần mở rộng hình ống trung tâm ở trung tâm của đầu trước của khối xylanh gắn vào thanh ngang phía trước của khung. Kết cấu này cho phép một số uốn cong của khung xe mà không gây ứng suất cho cấu trúc cơ bản của động cơ.
Mô tả sau đây về cấu tạo chung của động cơ chỉ ra các thành phần thiết yếu của động cơ piston-xylanh và giới thiệu danh pháp của các bộ phận khác nhau. Động cơ ô tô bốn kỳ được sử dụng làm loại cơ bản.
Khối Xylanh (Cylinder Block)
Thành phần cấu trúc chính của tất cả các động cơ ô tô là khối xylanh, thường kéo dài lên trên từ đường tâm của gối đỡ chính cho trục khuỷu đến điểm nối với nắp máy (cylinder head). Khối xylanh đóng vai trò là khung cấu trúc của động cơ và mang bệ lắp, nhờ đó động cơ được đỡ trong khung xe. Các động cơ máy phát điện tĩnh tại lớn và động cơ hàng hải được xây dựng từ một nền, hoặc bệ, và có cacte trên và dưới tách biệt với cụm xylanh.
Khối xylanh của động cơ ô tô là một vật đúc với các bề mặt gia công thích hợp và các lỗ ren để gắn nắp máy, ổ trục chính, cacte dầu và các bộ phận khác. Cacte được hình thành bởi phần của khối xylanh bên dưới lỗ xylanh và cacte dầu bằng kim loại dập hoặc đúc tạo thành phần bao dưới của động cơ và cũng đóng vai trò là bình chứa dầu bôi trơn, hoặc bể chứa.
Các xylanh là các lỗ có tiết diện tròn kéo dài qua phần trên của khối, với các thành bên trong được doa và đánh bóng để tạo thành các bề mặt ổ trục trơn tru, chính xác. Các xylanh của động cơ hạng nặng thường được trang bị các ống lót có thể tháo rời làm bằng kim loại có khả năng chống mài mòn tốt hơn so với kim loại được sử dụng trong vật đúc khối.
Có hai cách bố trí xylanh thông thường trong ô tô — loại thẳng hàng (in-line) (xem phần C của hình) và loại chữ V (xem phần D của hình).
- Động cơ thẳng hàng (in-line): Có một hàng xylanh duy nhất kéo dài theo chiều dọc lên trên từ cacte và thẳng hàng với các ổ trục chính của trục khuỷu.
- Động cơ chữ V: Có hai hàng xylanh, thường tạo thành một góc 60° hoặc 90° giữa hai dãy. Động cơ V8 (tám xylanh) thường là loại 90°. Một số động cơ máy bay sáu xylanh nhỏ có các xylanh nằm ngang đối đỉnh (xem ở trên Động cơ piston đối đỉnh).
Một đoạn đường khoan theo chiều dọc trong khối chứa trục cam vận hành các van. Vị trí của trục cam cho hầu hết các ứng dụng ô tô là ở trên cao — trục cam trên cao (OHC) hoặc trục cam kép trên cao (DOHC). Một khoang chứa bánh răng, xích hoặc đai cho bộ truyền động trục cam từ trục khuỷu được hình thành giữa đầu trước hoặc đầu sau của khối và một tấm che. Trên hầu như tất cả các động cơ hiện đại, một dây đai có răng được sử dụng để đảm bảo kiểm soát chính xác và đáp ứng của hệ thống truyền động van. Vỏ chuông được hình thành ở phía sau khối xylanh để bao quanh bánh đà và cung cấp cho việc gắn vỏ hộp số. Các áo nước được hình thành xung quanh các xylanh với các đoạn đường nối lõi thích hợp để lưu thông chất làm mát.
Thiết kế của khối xylanh bị ảnh hưởng bởi vị trí của các van của động cơ bốn kỳ và bởi việc cung cấp các cổng xylanh ở loại hai kỳ.
- Động cơ với xupap trên đỉnh (overhead-valve engine – OHV): Đã thay thế phần lớn loại L-head, có các van hoàn toàn nằm trong nắp máy.
- Động cơ L-head: Khối xylanh được mở rộng sang một bên của lỗ xylanh, với các đế van và các đoạn đường dẫn nạp và xả, cùng với các ống dẫn hướng van, được hình thành trong phần mở rộng này của khối. Nắp xylanh sau đó chỉ đơn thuần là một nắp có áo nước, cung cấp các vị trí ren cho bugi và với mặt dưới của nó được định hình sao cho một buồng đốt có kích thước và hình dạng mong muốn được hình thành phía trên mỗi lỗ xylanh.
Hình dạng của không gian tạo thành buồng đốt khi piston ở vị trí gần nhất với nắp máy và thể tích chứa trong đó so với thể tích dịch chuyển của piston là cực kỳ quan trọng trong ảnh hưởng của chúng đến hiệu suất. Nắp máy của động cơ có van đặt trong nắp máy hẹp hơn và sâu hơn, mang các đế van, ống dẫn hướng van và cổng van.
Buồng đốt
Buồng đốt được xác định bởi kích thước, vị trí và vị trí của piston bên trong xylanh.
- Đường kính xylanh (Bore): Đường kính trong của xylanh.
- Thể tích tại điểm chết dưới (VBDC): Thể tích giữa nắp máy và mặt piston khi piston ở xa nắp máy nhất.
- Thể tích tại điểm chết trên (VTDC): Thể tích khi piston ở gần nắp máy nhất; khoảng cách giữa mặt piston và nắp máy ở VTDC được gọi là khe hở.
- Hành trình (Stroke): Khoảng cách di chuyển của piston giữa các vị trí VTDC và VBDC.
- Tỷ số nén: Tỷ lệ giữa VTDC và VBDC được chuẩn hóa theo giá trị VTDC — tức là (VBDC/VTDC):1. Đây là yếu tố quan trọng nhất ảnh hưởng đến hiệu suất lý thuyết của chu trình động cơ.
Vì tăng tỷ số nén là cách tốt nhất để cải thiện hiệu suất, tỷ số nén trên động cơ ô tô có xu hướng tăng lên. Điều này đòi hỏi vật liệu bền và khỏe hơn. Trong thực tế, đặc tính bắt lửa của nhiên liệu, thường được biểu thị bằng chỉ số octan, giới hạn tỷ số nén của động cơ.
Piston
Piston là các chi tiết đúc hình trụ dạng cốc bằng thép hoặc hợp kim nhôm.
- Đỉnh piston (Crown): Đầu trên, kín, tạo thành bề mặt dưới của buồng đốt và nhận lực tác dụng từ khí cháy.
- Thân piston: Bề mặt ngoài được gia công để vừa khít với đường kính xylanh và có rãnh để lắp xéc măng (piston rings), làm kín khe hở giữa piston và thành xylanh.
- Xéc măng khí (Compression rings): Các vòng trên, kín, ngăn khí cháy lọt qua piston.
- Xéc măng dầu (Oil rings): Các vòng dưới, có lỗ, phân phối và hạn chế lượng dầu bôi trơn trên thành xylanh.
- Bạc chốt piston (Bosses): Được đúc ở hai bên đối diện của piston. Chốt piston bằng thép cứng được lắp vào các bạc này và xuyên qua đầu trên của thanh truyền (connecting rod).
Thanh truyền (Connecting Rod) và Trục khuỷu (Crankshaft)
- Thanh truyền: Bằng thép rèn, nối piston với một chốt khuỷu (phần lệch tâm) của trục khuỷu và chuyển đổi chuyển động tịnh tiến của piston thành chuyển động quay của trục khuỷu. Đầu dưới, lớn hơn, của thanh truyền được doa để lắp bạc lót chính xác được lót bằng babbit hoặc kim loại ổ trục khác và được lắp khít với chốt khuỷu. Động cơ kiểu chữ V thường có các xylanh đối diện so le đủ để cho phép hai thanh truyền hoạt động trên mỗi chốt khuỷu nằm cạnh nhau. Một số động cơ lớn hơn sử dụng thanh truyền dạng càng và lưỡi dao với các thanh truyền trong cùng mặt phẳng và các xylanh đối diện nhau.
- Trục khuỷu: Mỗi thanh truyền trong động cơ thẳng hàng hoặc mỗi cặp thanh truyền trong động cơ kiểu chữ V được gắn vào một chốt khuỷu của trục khuỷu. Mỗi chốt khuỷu bao gồm một chốt khuỷu (crankpin) với bề mặt ổ trục, trên đó lắp bạc lót thanh truyền và hai má hướng tâm (radial cheeks) nối nó với các phần của trục khuỷu quay trong các ổ trục chính, được đỡ bởi khối xylanh. Đủ số chốt khuỷu được cung cấp để phục vụ tất cả các xi lanh, và góc giữa chúng bằng khoảng thời gian đánh lửa góc giữa các xi lanh. Các chốt khuỷu của trục khuỷu động cơ sáu xi-lanh, bốn kỳ được đặt cách nhau 120° để sáu xi lanh nổ ở các khoảng thời gian bằng nhau trong hai vòng quay đầy đủ của trục. Các chốt của động cơ tám xi-lanh cách nhau 90°. Vị trí của mỗi chốt khuỷu dọc theo trục phụ thuộc vào thứ tự nổ của các xi lanh. Thứ tự nổ được chọn để phân phối các xung lực dọc theo chiều dài của động cơ để giảm thiểu rung động. Mô hình dòng chất lỏng trong ống nạp và ống xả cũng được xem xét. Thứ tự nổ tiêu chuẩn cho động cơ sáu xi-lanh là 1-5-3-6-2-4, điều này minh họa cho việc luân phiên các xung kế tiếp giữa các van phía trước và phía sau của động cơ bất cứ khi nào có thể. Cân bằng được cải thiện hơn nữa bằng cách thêm các đối trọng vào trục khuỷu để bù đắp khối lượng kim loại lệch tâm trong các chốt khuỷu.
Thiết kế trục khuỷu cũng thiết lập chiều dài hành trình piston vì độ lệch tâm hướng tâm của mỗi chốt khuỷu bằng một nửa hành trình truyền cho piston. Tỷ lệ giữa hành trình piston và đường kính xylanh là một yếu tố thiết kế quan trọng. Trong những năm đầu phát triển động cơ, không có cơ sở hợp lý nào cho việc thiết lập tỷ lệ này, và một phạm vi từ 1 đến 11/2 đã được các nhà sản xuất khác nhau sử dụng. Tuy nhiên, khi tốc độ động cơ tăng lên và rõ ràng là công suất ma sát tăng theo tốc độ piston chứ không phải theo tốc độ quay của trục khuỷu, đã bắt đầu một xu hướng hướng tới động cơ hành trình ngắn. Hành trình đã được rút ngắn xuống ít hơn 20% so với đường kính xylanh.
Từ yêu cầu đối với động cơ hai xylanh, có thể đưa ra một quy tắc chung cho cách bố trí các chốt khuỷu của trục khuỷu nhiều xylanh bốn kỳ. Bất kể số lượng xylanh, hai piston phải đến điểm chết trên cùng một lúc để xylanh thứ hai sẵn sàng nổ chính xác 360° sau khi mỗi xylanh nổ. Một nửa số xylanh sau đó sẽ nổ trong mỗi vòng quay của trục khuỷu. Để tuân theo quy tắc này, phải có một số lượng xylanh chẵn để có thể có các cặp xylanh có piston di chuyển đồng bộ.
Một động cơ tám xi-lanh nổ mỗi khi trục khuỷu của nó quay một phần tư vòng nếu khoảng thời gian giữa các xung là bằng nhau. Trục khuỷu cho động cơ tám xi-lanh, thẳng hàng được thiết kế với mỗi trong số tám chốt khuỷu của nó cách một phần tư vòng so với một chốt khuỷu khác.
Để cân bằng chiều dọc tốt nhất, các xi lanh có piston cùng pha là xi lanh đầu tiên và cuối cùng của động cơ thẳng hàng, xi lanh thứ hai và gần cuối cùng, tiếp tục theo thứ tự đó với các chốt khuỷu thẳng hàng cách đều tâm động cơ.
Van (Valves), Đũa đẩy (Pushrods), và Cò mổ (Rocker Arms)
- Van (Valves): Để điều khiển nạp và xả, van có thể được đặt trên cao (overhead), ở một bên, ở một bên và trên cao, hoặc ở hai bên đối diện của xylanh. Đây đều là các van kiểu nấm (poppet valve), bao gồm một thân van với một đầu được mở rộng để tạo thành một đầu van cho phép dòng chảy đi qua một đoạn bao quanh thân van khi được nâng lên khỏi đế của nó và ngăn dòng chảy khi đầu van được hạ xuống để tiếp xúc với đế van được tạo thành trong khối xylanh. Một nhóm động cơ khác sử dụng van trượt thường là loại ống lót bao quanh lỗ xylanh.
- Cơ cấu truyền động xupap trên cao OHV:
- Đũa đẩy (Pushrods): Động cơ có van đặt trong nắp máy có các đũa đẩy kéo dài lên trên từ con đội (cam followers) đến cò mổ (rocker arms) được gắn trên nắp máy, tiếp xúc với thân van và truyền chuyển động do biên dạng cam tạo ra đến các van.
- Cò mổ (Rocker arms):
- Khe hở xupap (Tappet clearance): Khe hở phải được duy trì giữa các đầu của thân van và cơ cấu nâng để đảm bảo đóng van đúng cách khi nhiệt độ động cơ thay đổi. Điều này được thực hiện bằng cách điều chỉnh chiều dài đũa đẩy hoặc bằng cách sử dụng con đội thủy lực.
- Con đội thủy lực (Hydraulic lifters): Loại bỏ tiếng ồn và hoạt động không ổn định của van.
- Cấu tạo: Bao gồm một con đội được cam đẩy lên xuống, và một lỗ bên trong có chứa một cốc đội van (valve lifter) được lắp khít và giữ bằng một kẹp lò xo. Cốc đội van, đến lượt nó, là một cốc được đóng ở phía trên bằng một nút hình trụ chuyển động tự do có một ổ cắm ở phía trên để vừa với đầu dưới của đũa đẩy. Nút này được đẩy lên trên bằng một lò xo nhẹ có khả năng lấy khe hở giữa thân van và cò mổ.
- Nguyên lý: Một lỗ nhỏ được khoan ở đáy cốc đội van để cho phép dầu bôi trơn đi vào con đội từ hệ thống bôi trơn của động cơ thông qua một đường dẫn trong khối xylanh. Một viên bi thép nhỏ đóng vai trò là van một chiều để cho phép dầu vào cốc đội van nhưng ngăn không cho nó thoát ra ngoài. Khi khe hở trong toàn bộ liên kết giữa biên dạng cam và thân van được lò xo trong cốc đội van thu lại, dầu chảy vào buồng đội, qua van bi một chiều và bị giữ lại ở đó để duy trì tình trạng không có khe hở này khi động cơ hoạt động. Sự giãn nở hoặc co lại của liên kết van được bù bằng cách rò rỉ dầu từ bộ nâng để điều chỉnh sự giãn nở của các bộ phận và dòng dầu vào buồng nếu có xu hướng tạo ra khe hở giữa đũa đẩy và con đội. Việc đóng hoàn toàn van sau đó được đảm bảo mọi lúc mà không có tiếng ồn của con đội.
Van nạp phải mở trong khi piston đang đi xuống trong kỳ nạp của piston, và van xả phải mở trong khi piston đang đi lên trong kỳ xả. Do đó, có vẻ như việc đóng và mở hai van sẽ xảy ra tại các điểm chết trên và dưới thích hợp của trục khuỷu. Tuy nhiên, thời gian cần thiết để các van đóng và mở, và ảnh hưởng của tốc độ cao đến việc bắt đầu và dừng dòng chảy của khí đòi hỏi rằng để có hiệu suất tối ưu, các sự kiện mở xảy ra trước các vị trí điểm chết của trục khuỷu và các sự kiện đóng bị trì hoãn cho đến sau điểm chết.
Do đó, cả bốn sự kiện van — mở van nạp, đóng van nạp, mở van xả và đóng van xả — được dịch chuyển một cách đáng kể so với điểm chết trên và dưới. Các sự kiện mở sớm hơn và các sự kiện đóng muộn hơn để cho phép các đoạn đường dốc (ramps) được kết hợp trong biên dạng cam để cho phép mở dần dần ban đầu và đóng dần cuối cùng để tránh va đập của van. Các đường dốc được cung cấp để bắt đầu nâng dần dần và làm chậm van trước khi nó tiếp xúc với đế của nó. Mở sớm và đóng muộn cũng nhằm mục đích sử dụng quán tính hoặc sự bền bỉ của dòng khí để hỗ trợ làm đầy và làm rỗng xylanh.
Trục cam (Camshaft)
Trục cam, đóng và mở các van, được dẫn động từ trục khuỷu bằng bộ truyền động xích hoặc bánh răng ở đầu trước của động cơ. Bởi vì một vòng quay của trục cam hoàn thành hoạt động của van cho toàn bộ một chu trình của động cơ và động cơ bốn kỳ thực hiện hai vòng quay trục khuỷu để hoàn thành một chu trình, trục cam quay chậm bằng một nửa tốc độ trục khuỷu.
- Vị trí: Nó nằm phía trên và lệch về một bên của trục khuỷu, đặt nó ngay dưới các van của động cơ L-head hoặc các đũa đẩy kéo dài xuống từ cò mổ của động cơ có van đặt trên nắp máy (OHV).
- Giới hạn tốc độ (động cơ OHV): Do các đũa đẩy dài và cò mổ, tốc độ của động cơ OHV bị giới hạn ở tốc độ mà con đội (cam followers) có thể duy trì tiếp xúc với cam khi các van đang đóng. Trên tốc độ giới hạn đó, các van được cho là “nổi” (float), và chuyển động của chúng có xu hướng trở nên thất thường.
- Trục cam trên cao (Overhead-camshaft engine – OHC): Vì lý do này, động cơ trục cam trên cao (OHC) khá phổ biến. Nằm ngay phía trên các van, loại trục cam này được dẫn động bằng trục đứng và bánh răng côn hoặc bằng dây đai răng.
Bánh đà (Flywheel)
Chu trình của động cơ đốt trong là lực xoắn (mô-men xoắn) chỉ được tác dụng không liên tục khi mỗi xylanh nổ. Giữa các xung lực này, các piston đi lên trong kỳ nén và lực cản quay do tải trọng mà động cơ mang gây ra mô-men xoắn âm. Gia tốc xen kẽ do xung lực và giảm tốc do nén dẫn đến chuyển động quay không đều.
Để chống lại xu hướng chậm lại và tăng tốc này, bánh đà được gắn vào một đầu của trục khuỷu. Bánh đà bao gồm một đĩa gang hình tròn nặng với một moay ơ để gắn vào động cơ. Khối lượng quay nặng của nó có đủ động lượng để chống lại tất cả các thay đổi về tốc độ quay của nó và buộc trục khuỷu quay đều ở tốc độ này. Do đó, động cơ chạy trơn tru mà không có dấu hiệu dao động quay. Vành ngoài của bánh đà thường mang răng bánh răng để khớp với động cơ khởi động (mô-tơ đề). Thành phần truyền động của ly hợp hoặc khớp nối chất lỏng (biến mô) cho hộp số có thể được tích hợp trong bánh đà.
Ổ trục (Bearings)
Trục khuỷu có các bề mặt ổ trục trên mỗi chốt khuỷu và ba hoặc nhiều ổ trục chính. Chúng chịu tải nặng do lực tịnh tiến tại mỗi xylanh tác dụng lên trục khuỷu và trọng lượng của trục khuỷu và bánh đà.
Tất cả trừ các động cơ nhỏ nhất đều sử dụng ổ trục dạng vỏ tách, thường được làm bằng đồng với lớp lót bằng kim loại babbit. Vật liệu bề mặt đủ mềm để giảm thiểu khả năng làm xước trục khuỷu trong trường hợp bôi trơn không đủ. Các động cơ nhỏ nhất thường có ổ trục bằng gang babbit đúc. Một khoảng hở ổ trục nhỏ là cần thiết để cho phép một màng dầu tách các bề mặt.
Hệ thống đánh lửa
Phân loại hệ thống đánh lửa
Hệ thống đánh lửa điện có thể được phân loại thành hệ thống magneto, ắc quy-cuộn dây và hệ thống đánh lửa trạng thái rắn (solid-state). Mặc dù chúng tương tự nhau về nguyên tắc cơ bản, magneto là hệ thống khép kín và chỉ yêu cầu bugi và dây kết nối để hoàn thành hệ thống, trong khi hệ thống ắc quy-cuộn dây và hệ thống đánh lửa trạng thái rắn bao gồm một số thành phần riêng biệt.
- Magneto: Là một máy phát điện xoay chiều nam châm cố định được thiết kế để tạo ra đủ điện áp để đánh lửa bugi. Một magneto cao áp hoàn toàn khép kín và chỉ yêu cầu bugi, dây điện và công tắc để đáp ứng các yêu cầu đánh lửa.
- Hệ thống ắc quy và cuộn dây (Battery-and-coil): Bao gồm một ắc quy, một cực được nối đất trong khi cực còn lại dẫn qua một công tắc đến cuộn dây sơ cấp của cuộn dây (bobine), và sau đó đến một bộ ngắt mạch nơi nó lại được nối đất. Sự quay của cam ngắt mạch đóng và mở mạch sơ cấp. Mạch thứ cấp, bao gồm vài nghìn vòng dây mịn, dẫn đến rotor của bộ chia điện, hoạt động như một công tắc xoay, chọn bugi được đưa vào mạch. Mỗi bugi được kết nối với một trong các cực bên ngoài của bộ chia điện để nhận xung điện theo trình tự thích hợp. Khi mạch sơ cấp bị ngắt, một điện thế cao (lên đến 20.000 vôn) được phát triển trong cuộn dây thứ cấp và được dẫn đến bugi thích hợp.
- Hệ thống đánh lửa phóng điện tụ (Capacitor discharge ignition system): Điện áp cao cho bugi cũng có thể được tạo ra bởi hệ thống này. Một hệ thống như vậy bao gồm một nguồn điện một chiều 250 đến 300 vôn được cấp cho một tụ điện lưu trữ, một thiết bị để lưu trữ điện tích. Một dây dẫn từ tụ điện đi đến một phía của cuộn dây sơ cấp của bugi thông qua các tiếp điểm ngắt mạch được kích hoạt bằng cam hoặc một thiết bị chuyển mạch điện tử. Ngay khi thiết bị chuyển mạch này thiết lập tiếp xúc, tụ điện phóng điện qua cuộn sơ cấp của cuộn đánh lửa, và một điện áp cao tức thời được đưa đến bộ chia điện và sau đó đến bugi. Hệ thống phóng điện tụ cung cấp tia lửa mạnh hơn, do đó cải thiện khả năng khởi động của động cơ lạnh hoặc ngập xăng. Nó tiếp tục đánh lửa các bugi khi chúng bị bám bẩn bởi carbon hoặc các chất lắng đọng khác hoặc khi khe hở đánh lửa đã mở rộng do sự ăn mòn của các điểm. Các ưu điểm đáng chú ý khác bao gồm tăng tuổi thọ bugi, cải thiện khả năng đánh lửa trên phạm vi tốc độ rộng hơn và khả năng chịu ẩm tốt hơn.
- Hệ thống đánh lửa trạng thái rắn (Solid-state): Không giống như các hệ thống ắc quy và cuộn dây sử dụng bộ chia điện, sử dụng một mô-đun điện tử để thu thập thông tin từ các cảm biến động cơ, tính toán các thông số hoạt động của động cơ và điều khiển phóng điện đánh lửa đến một cuộn dây riêng cho mỗi bugi. Mô-đun điều khiển điện tử kích hoạt một bóng bán dẫn để ngắt mạch nối đất dẫn đến cuộn dây của mỗi bugi, do đó gây ra tia lửa. Ngoài việc loại bỏ các dây bugi cao áp, thiết bị điện tử cho phép kiểm soát chính xác hơn thời điểm đánh lửa, giúp cải thiện hiệu suất nhiên liệu, giảm lượng khí thải và tăng công suất.
Bugi (Spark plugs)
Bugi là một bộ phận quan trọng của hệ thống đánh lửa và là bộ phận phải hoạt động trong điều kiện khắc nghiệt nhất. Vì tiếp xúc với nhiệt độ và áp suất buồng đốt, cũng như các chất bẩn sinh ra trong quá trình cháy, bugi cần được bảo dưỡng thường xuyên hơn và thường là bộ phận “yểu mệnh” nhất của động cơ xăng. Nó bao gồm một vỏ thép có ren để vừa với lỗ tiêu chuẩn 14 mm trên nắp máy (cylinder head). Bugi có thể sử dụng vòng đệm (gasket) hoặc mặt côn (tapered seat) để đảm bảo kín khí giữa nắp máy và bugi. Một lõi cách điện bằng gốm được đúc vào thân bugi, và điện cực trung tâm (centre electrode) bằng thép xuyên qua lớp cách điện lên đến đầu nối, nơi gắn dây cao áp (high-voltage lead) từ bộ chia điện (distributor). Điện cực còn lại được hàn vào thân kim loại của bugi, được nối đất (grounded) với nắp máy. Điện cực có nhiều hình dạng khác nhau và được làm từ nhiều loại hợp kim.
Khi sử dụng, điều quan trọng là khe hở bugi (spark gap) phải đúng theo thông số kỹ thuật của từng động cơ. Có sẵn các dụng cụ đo để điều chỉnh khe hở này bằng cách uốn điện cực nối đất khi cần. Các nhà sản xuất quy định khe hở từ 0,508 đến 1,016 mm giữa điện cực trung tâm và điện cực nối đất. Nếu khe hở bugi quá lớn, khả năng đánh lửa sai (misfiring) tăng lên. Nếu khe hở quá nhỏ, tia lửa sẽ không đủ mạnh. Sự tăng khe hở do mòn điện cực có thể được điều chỉnh. Bugi hiện đại thường tích hợp điện trở để giảm thiểu phát xạ tần số vô tuyến (radio frequency emissions) có thể gây nhiễu cho các thiết bị điện tử nhạy cảm.
Bộ chế hòa khí (Carburetor)
Bộ chế hòa khí là thiết bị đưa nhiên liệu vào dòng khí khi nó đi vào động cơ. Xăng được giữ trong buồng phao (float chamber) nhờ van phao (float-actuated valve) ở mức thấp hơn một chút so với đầu ra của tia phun (jet). Không khí đi xuống qua họng (throat), qua van tiết lưu (throttle valve) và vào ống nạp (intake manifold). Họng được tạo thành bởi đường kính giảm, và sự tăng tốc của không khí qua đoạn hẹp này gây ra sự giảm áp suất tỷ lệ với lượng không khí đi qua. Sự giảm áp suất này ở họng dẫn đến xăng chảy từ tia phun vào dòng khí. Bất kỳ sự tăng lưu lượng khí nào do thay đổi tốc độ động cơ hoặc vị trí van tiết lưu đều làm tăng chênh lệch áp suất tác động lên nhiên liệu và khiến nhiều nhiên liệu chảy hơn.
Tỷ lệ thể tích của nhiên liệu so với không khí được thiết lập bởi kích thước họng và tia phun sẽ được duy trì khi lưu lượng tăng, nhưng tỷ lệ khối lượng của nhiên liệu so với không khí tăng lên vì không khí giãn nở đến mật độ thấp hơn khi áp suất họng giảm. Xu hướng làm đậm hỗn hợp (enriching tendency) này đòi hỏi phải có một thiết bị bù (compensating device) trong bộ chế hòa khí thực tế. Thiết kế bộ chế hòa khí phức tạp hơn nữa do cần có một thiết bị làm đậm hỗn hợp để cung cấp tỷ lệ công suất tối đa (maximum-power ratio) khi mở hết ga (full throttle), một le gió (choke) để dễ khởi động động cơ nguội, một hệ thống không tải (idling system) để đáp ứng các nhu cầu đặc biệt khi hoạt động tải nhẹ, và một thiết bị tăng tốc (accelerating device) để cung cấp thêm nhiên liệu khi đang mở ga.
Phun xăng điện tử (Fuel injection)
Hầu hết các động cơ ô tô hiện đại sử dụng hệ thống phun xăng điện tử (electronic fuel-injection system) trong ống nạp (intake manifold) của động cơ thay vì bộ chế hòa khí. Hệ thống phun xăng là một hệ thống phản hồi vòng kín (closed-loop feedback system) được điều khiển bởi một hệ thống quản lý động cơ (engine management system) bao gồm các cảm biến (sensors), bơm xăng điện (electric fuel pump), kim phun (fuel injectors), ống dẫn nhiên liệu (fuel tubing) và van. Hệ thống quản lý động cơ kiểm soát cả việc đánh lửa và quản lý nhiên liệu. Trong một số thiết kế, hệ thống quản lý động cơ cũng kiểm soát cả hộp số. Các cảm biến theo dõi hoạt động của động cơ và các điều kiện môi trường và truyền dữ liệu đến hệ thống quản lý động cơ để xác định lượng nhiên liệu cần bơm đến kim phun để cung cấp cho động cơ. Các cảm biến điển hình bao gồm: lưu lượng khí nạp (mass airflow), ôxy khí xả (exhaust oxygen), vòng tua máy (engine revolutions per minute), áp suất tuyệt đối ống nạp (manifold absolute pressure), áp suất khí quyển (barometric pressure), nhiệt độ nước làm mát (coolant temperature), vị trí bướm ga (throttle position), kích nổ (knock), tốc độ xe (vehicle speed), tải điều hòa (air-conditioning load), tải trợ lực lái (power steering load), vị trí trục khuỷu (crankshaft position) và vị trí trục cam (camshaft position).
Ưu điểm chính của phun xăng so với bộ chế hòa khí là tiết kiệm nhiên liệu hơn do tỷ lệ nhiên liệu và không khí chính xác hơn, công suất lớn hơn do loại bỏ việc sấy nhiên liệu, loại bỏ đóng băng đường nạp, và cung cấp nhiên liệu đồng đều và trực tiếp hơn đến các xi-lanh. Vì phun xăng không dựa vào chân không ống nạp (intake manifold vacuum) để cung cấp nhiên liệu, phun xăng điện tử được sử dụng với động cơ tăng áp (turbocharged engines).
Siêu nạp (Supercharger)
Hiệu suất của quá trình nạp trong động cơ ô tô thường tăng lên đến đỉnh điểm hơn 80% một chút ở khoảng một nửa tốc độ định mức của động cơ và sau đó giảm đáng kể ở tốc độ cao hơn. Sự thay đổi lượng khí nạp này theo tốc độ động cơ được phản ánh trong những thay đổi tỷ lệ thuận của mô-men xoắn (torque), hoặc lực xoay, tác dụng lên trục khuỷu và làm cho công suất mà động cơ có thể cung cấp khi mở hết ga đạt mức tối đa khi tốc độ động cơ tăng. Ở tốc độ cao hơn tốc độ đỉnh này, lượng khí nạp vào mỗi chu kỳ giảm nhanh đến mức công suất tạo ra ít hơn so với ở tốc độ thấp hơn. Việc động cơ không thể nạp đầy không khí sạch ở tốc độ cao sẽ giới hạn công suất đầu ra của động cơ.
Siêu nạp khắc phục nhược điểm này bằng cách sử dụng một máy bơm hoặc máy thổi (blower) để tăng áp suất không khí cung cấp cho các xi-lanh và tăng khối lượng nạp. Sự sụt giảm công suất mà động cơ không siêu nạp gặp phải ở độ cao lớn (ví dụ: khi bay hoặc lái xe qua núi) có thể được phục hồi phần lớn. Cũng có thể tăng gấp đôi công suất của động cơ bằng cách siêu nạp; tuy nhiên, mật độ và nhiệt độ nạp tăng lên, do siêu nạp, làm tăng xu hướng kích nổ (combustion knock) hoặc nổ không êm (roughness) trong động cơ đánh lửa bằng tia lửa điện và do đó cần phải giảm tỷ số nén (compression ratio) một cách không mong muốn hoặc sử dụng nhiên liệu chống kích nổ (antiknock fuel).
Máy thổi siêu nạp có thể được nối với trục khuỷu bằng bánh răng, trong trường hợp đó, công suất tiêu thụ để truyền động nó được cộng vào tổn thất ma sát của động cơ. Bộ tăng áp (turbocharger) sử dụng một tua-bin khí (gas turbine) hoạt động bằng khí thải để truyền động một máy thổi ly tâm (centrifugal blower). Động cơ tăng áp không chỉ tăng công suất mà còn hoạt động tiết kiệm nhiên liệu hơn. Trong lịch sử, các động cơ xăng máy bay lớn thường được siêu nạp bằng cả máy thổi có bánh răng và bộ tăng áp để cung cấp khả năng bơm lớn cần thiết ở độ cao lớn; tuy nhiên, những động cơ này thường được thay thế bằng động cơ tuabin cánh quạt (turboprop engines). Máy bay hàng không đa dụng hiệu suất cao thường sử dụng động cơ tăng áp.
Vì việc nén không khí trước khi đưa vào xi-lanh làm tăng nhiệt độ không khí nạp, khối lượng không khí có thể được đưa vào động cơ ít hơn so với khi không khí nén ở nhiệt độ môi trường. Do đó, bộ làm mát không khí nạp của động cơ, thường được gọi là bộ làm mát trung gian (intercoolers) hoặc bộ làm mát sau (aftercoolers), được sử dụng để giảm nhiệt độ của không khí nạp. Có sẵn cả loại làm mát bằng chất lỏng (air-to-coolant) và loại làm mát bằng không khí (air-to-air).
Hệ thống làm mát (Cooling system)
Xi-lanh của động cơ đốt trong cần được làm mát vì động cơ không thể chuyển hóa toàn bộ năng lượng sinh ra từ quá trình đốt cháy thành công có ích. Làm mát bằng chất lỏng (Liquid cooling) được sử dụng trong hầu hết các động cơ xăng, cho dù động cơ dùng cho ô tô hay các mục đích khác. Chất lỏng được tuần hoàn xung quanh các xi-lanh để hấp thụ nhiệt và sau đó qua bộ tản nhiệt (radiator) để tỏa nhiệt. Thông thường, một van hằng nhiệt (thermostat) được đặt trong hệ thống tuần hoàn để duy trì nhiệt độ áo nước (jacket temperature) theo thiết kế—khoảng 88 °C (190 °F). Hệ thống làm mát thường được điều áp (pressurized) để tăng điểm sôi của chất làm mát, nhờ đó có thể duy trì nhiệt độ đầu ra cao hơn để cải thiện hiệu suất nhiệt và tăng khả năng truyền nhiệt của bộ tản nhiệt. Nắp áp suất (pressure cap) trên bộ tản nhiệt duy trì áp suất này bằng các van mở ra ngoài ở áp suất thiết kế và mở vào trong để ngăn chân không khi hệ thống nguội đi.
Một số động cơ, đặc biệt là động cơ máy bay và các thiết bị nhỏ cho máy cắt cỏ, cưa xích và các công cụ khác, được làm mát bằng không khí (air-cooled). Làm mát bằng không khí được thực hiện bằng cách tạo các cánh tản nhiệt (fins) kim loại mỏng trên bề mặt bên ngoài của xi-lanh để tăng tốc độ truyền nhiệt bằng cách tăng diện tích bề mặt kim loại tiếp xúc với không khí làm mát. Không khí được ép buộc lưu thông nhanh qua các khoảng trống giữa các cánh tản nhiệt bằng cách dẫn khí về phía động cơ.
Hệ thống bôi trơn (Lubrication system)
Bôi trơn được sử dụng để giảm ma sát bằng cách tạo một lớp màng giữa các bộ phận cọ xát. Hệ thống bôi trơn phải liên tục thay thế lớp màng này.
Các chất bôi trơn thường được sử dụng được tinh chế từ dầu thô sau khi đã loại bỏ nhiên liệu. Độ nhớt (viscosities) của chúng phải phù hợp với từng động cơ và dầu phải phù hợp với mức độ khắc nghiệt của điều kiện vận hành. Dầu được cải tiến bằng các chất phụ gia (additives) giúp giảm quá trình oxy hóa, ức chế ăn mòn và hoạt động như chất tẩy rửa (detergents) để phân tán cặn bẩn dạng keo và chất rắn. Dầu động cơ cũng bao gồm chất chống tạo bọt (antifoaming agent). Các hệ thống số khác nhau được sử dụng để chỉ định độ nhớt của dầu; số càng thấp, dầu càng loãng. Độ nhớt phải được chọn để phù hợp với tốc độ dòng chảy của dầu qua một bộ phận với các yêu cầu làm mát theo thiết kế của bộ phận đó. Nếu dầu quá đặc, nó sẽ không chảy qua bộ phận đủ nhanh để tản nhiệt đúng cách. Một số loại dầu có chứa các chất phụ gia chống lại sự thay đổi độ nhớt giữa mùa đông và mùa hè.
Bộ lọc dầu (Oil filters), nếu được bảo dưỡng thường xuyên, có thể loại bỏ các chất bẩn rắn khỏi dầu cacte (crankcase oil), nhưng các phản ứng hóa học có thể tạo thành các chất lỏng ăn mòn và gây hại. Sự suy giảm các chất phụ gia cũng giới hạn tuổi thọ của dầu bôi trơn.
Hệ thống bôi trơn được cấp dầu từ cacte dầu (oil sump), tạo thành phần bao bọc phía dưới của động cơ. Dầu được lấy từ cacte bằng một máy bơm (pump), thường là loại bánh răng (gear type), và được đưa qua bộ lọc và được cung cấp dưới áp suất đến một hệ thống các đường dẫn hoặc rãnh được khoan xuyên qua động cơ. Hầu như tất cả các động cơ hiện đại đều sử dụng bộ lọc dầu kiểu toàn dòng (full-flow type). Dầu đã lọc được cung cấp dưới áp suất đến các ổ trục chính của trục khuỷu và trục cam. Các khuỷu liền kề được khoan để cho phép dầu chảy từ nguồn cung cấp ở ổ trục chính đến chốt khuỷu. Dầu rò rỉ từ tất cả các ổ trục khuỷu được phun lên thành xi-lanh, cam và lên pít-tông để bôi trơn chốt pít-tông (piston pins). Các đường dẫn bổ sung giao nhau với các lỗ mở của con đội (cam-follower) và cung cấp dầu cho các bộ nâng van thủy lực (hydraulic valve lifters) khi được sử dụng. Một van giảm áp (pressure-relief valve) có lò xo duy trì áp suất ở mức thích hợp. Dầu rất quan trọng cho cả việc bôi trơn và làm mát.
Hệ thống xả (Exhaust system)
Sản phẩm cháy thoát ra khỏi xi-lanh động cơ qua các van xả (exhaust valves) trong nắp máy (cylinder head). Động cơ có thể được cấu hình với cổ xả (exhaust manifold) hoặc pô độ (exhaust header). Cổ xả là một buồng chung mà tất cả các xi-lanh trực tiếp đưa sản phẩm cháy vào. Ưu điểm của phương pháp này là đơn giản trong sản xuất và bố trí. Nhược điểm là áp suất ngược (backpressure) không đều tại các cổng xả của xi-lanh. Pô độ bao gồm một nhóm các ống, tất cả có cùng chiều dài, được nối một đầu với từng vị trí van xả của xi-lanh và đầu kia với một họng xả chung.
Khí thải trong động cơ ô tô hiện đại tiếp theo đi qua một thiết bị kiểm soát khí thải (emission-control device). Các cảm biến kiểm soát khí thải và bộ chuyển đổi xúc tác (catalytic converters) để giảm ô nhiễm không khí là các thành phần bổ sung của hệ thống xả. Thông thường, khí thải đi vào bộ chuyển đổi xúc tác để giảm lượng khí thải nitơ oxit (nitric oxide). Buồng tiếp theo làm giảm lượng khí thải hydrocacbon chưa cháy hết (unburned hydrocarbons) và carbon monoxide.
Hệ thống phản ứng (reactor system) để kiểm soát khí thải thường bao gồm một máy nén khí (air compressor) được dẫn động bằng dây đai (belt-driven) nối với các vòi phun nhỏ (nozzles) được lắp đặt trong ống xả đối diện với đầu ra của mỗi van xả. Một tia khí nhỏ được hướng về phía dòng sản phẩm cháy nóng đỏ để cung cấp oxy để đốt cháy hydrocacbon và carbon monoxide. Các cảm biến theo dõi các thông số khí thải (ví dụ: nhiệt độ và hàm lượng oxy) và, trong hệ thống phun xăng điện tử, cung cấp thông tin cho bộ điều khiển (control unit) để hỗ trợ giảm lượng khí thải gây ô nhiễm.
Khí thải từ động cơ đốt trong được đưa qua bộ giảm thanh (muffler) để triệt tiêu các rung động âm thanh. Khi van xả mở, áp suất trong động cơ làm cho khí ban đầu thoát ra với tốc độ bùng nổ. Các lần xả liên tiếp từ các xi-lanh tạo ra các xung áp suất (pressure pulsations) tạo ra âm thanh chói tai. Bộ giảm thanh làm suy giảm hoặc hấp thụ các xung này để khí thoát ra khỏi cửa xả như một dòng chảy tương đối êm và tĩnh lặng.
Các bộ giảm thanh thiết kế ban đầu chứa các bộ vách ngăn (baffles) làm đảo ngược dòng khí hoặc khiến chúng đi theo những con đường vòng vèo để sự giao thoa giữa các sóng áp suất làm giảm các xung. Các bộ giảm thanh thường được sử dụng nhất trong các phương tiện cơ giới hiện đại sử dụng các buồng cộng hưởng (resonating chambers) được kết nối với các đường dẫn mà khí đi qua. Các rung động khí được thiết lập trong mỗi buồng này ở tần số cơ bản (fundamental frequency) được xác định bởi kích thước của nó. Những rung động này triệt tiêu hoặc hấp thụ những rung động có trong dòng khí thải có cùng tần số. Một số buồng như vậy, mỗi buồng được điều chỉnh theo một trong những tần số chủ đạo có trong dòng khí thải, giúp giảm tiếng ồn một cách hiệu quả.
Nhiên liệu (Fuel)
Xăng ban đầu được coi là nguy hiểm và bị loại bỏ, tiêu hủy tại các nhà máy lọc dầu thời kỳ đầu, vốn sản xuất dầu hỏa (kerosene) cho đèn. Khi động cơ xăng phát triển, xăng và động cơ đã được “hòa hợp” để đạt được sự phù hợp tốt nhất về đặc tính. Các đặc tính quan trọng nhất của xăng là độ bay hơi (volatility) và khả năng chống kích nổ (antiknock quality). Độ bay hơi là thước đo mức độ dễ bay hơi của xăng, được điều chỉnh trong quá trình sản xuất để phù hợp với sự thay đổi theo mùa và độ cao ở thị trường địa phương. Xăng có công thức phù hợp giúp động cơ khởi động trong thời tiết lạnh và tránh hiện tượng khóa hơi (vapor lock) trong thời tiết nóng.
Để phù hợp với nhu cầu của động cơ hiện đại, xăng phải có độ bay hơi mà hệ thống nhiên liệu của động cơ được thiết kế và chất lượng chống kích nổ đủ để tránh kích nổ trong quá trình hoạt động bình thường. Mặc dù các thông số kỹ thuật khác cũng phải được đáp ứng, độ bay hơi và chỉ số chống kích nổ là quan trọng nhất. Kích thước và sự sắp xếp cấu trúc của các phân tử chủ yếu quyết định xu hướng kích nổ của xăng cũng như độ bay hơi của nó.
Tetraethyl chì (Tetraethyl lead), được thêm vào xăng trong nhiều năm để cải thiện khả năng chống kích nổ, đã được phát hiện là gây ô nhiễm khí thải bằng các oxit chì độc hại, và do đó, việc sử dụng nó đã chấm dứt. Tỷ số nén thấp hơn và thiết kế buồng đốt cải tiến đã loại bỏ nhu cầu về xăng có chỉ số chống kích nổ cực cao.
Dầu bôi trơn được thêm vào xăng dùng trong động cơ hai kỳ nén cacte (crankcase-compression).
Hiệu suất (Performance)
Hiệu suất của động cơ được thể hiện bằng công suất (power), tốc độ (speed) và mức tiết kiệm nhiên liệu (fuel economy). Ba đại lượng này được đánh giá bằng lực kế (dynamometer), một thiết bị thí nghiệm tạo ra tải có thể điều khiển được dưới dạng lực cản đối với chuyển động quay của trục khuỷu và cũng đo mô-men xoắn (torque) tác dụng tại khớp nối trục. Lực cản do lực kế tạo ra có thể được điều chỉnh để thiết lập tốc độ động cơ mong muốn ở bất kỳ vị trí bướm ga nào. Do đó, có thể chạy động cơ ở nhiều tốc độ khác nhau trong phạm vi hoạt động của nó, liên tục duy trì các điều kiện vận hành này và đo chính xác tải và tốc độ ở mỗi lần chạy. Thiết bị kiểm tra bổ sung cho phép đo lượng nhiên liệu tiêu thụ chính xác, cũng như thời gian chạy. Từ những dữ liệu này, có thể tính toán các mối quan hệ công suất-tốc độ-tiết kiệm và vẽ đồ thị hiệu suất.
Công suất do động cơ tạo ra được tính bằng mã lực (horsepower). Khi công suất được đo bằng lực kế hoặc thiết bị hãm tương tự, nó được gọi là mã lực phanh (brake horsepower). Đây là công suất thực tế do động cơ cung cấp và do đó là công suất của động cơ. Công suất được tạo ra trong buồng đốt của động cơ lớn hơn công suất cung cấp do ma sát và các tổn thất cơ học khác. Sự mất mát công suất này, được gọi là mã lực ma sát (friction horsepower), có thể được đánh giá bằng cách “kéo” động cơ (quay theo chiều thuận) bằng một lực kế phù hợp khi không có nhiên liệu nào được đốt cháy. Công suất được tạo ra trong xi-lanh sau đó có thể được tìm thấy bằng cách cộng mã lực ma sát với mã lực phanh. Đại lượng này là mã lực chỉ thị (indicated horsepower) của động cơ, được gọi tên theo một thiết bị được gọi là bộ chỉ thị động cơ (engine indicator), được sử dụng để đo áp suất lên pít-tông và do đó tính toán công suất được tạo ra trong xi-lanh.
Hiệu suất cơ học (Mechanical efficiency) được định nghĩa là mã lực phanh tính theo phần trăm mã lực chỉ thị và thường nằm trong khoảng từ 70 đến 90 phần trăm đối với tốc độ hoạt động bình thường.
Một đại lượng gọi là áp suất hiệu dụng trung bình phanh (brake mean effective pressure) thu được bằng cách nhân áp suất hiệu dụng trung bình (mean effective pressure) của động cơ với hiệu suất cơ học của nó. Đây là một chỉ số thường được sử dụng để biểu thị khả năng của động cơ, trên một đơn vị đường kính xi-lanh, để tạo ra cả áp suất hữu ích trong xi-lanh và công suất cung cấp. Nếu công suất cung cấp được tăng lên bằng bất kỳ thay đổi nào khác ngoài việc tăng tốc độ hoặc kích thước xi-lanh, áp suất hiệu dụng trung bình phanh của nó sẽ tăng tương ứng.
So sánh với các loại động cơ khác
Khi so sánh động cơ xăng với các loại động cơ đốt trong khác, một số điểm tương đồng và khác biệt, cũng như một số ưu điểm và nhược điểm, trở nên rõ ràng. Động cơ diesel và động cơ khí (động cơ sử dụng khí như khí tự nhiên nén hoặc propan làm nhiên liệu) có nhiều điểm chung với động cơ xăng, vì tất cả chúng đều là động cơ xi-lanh và pít-tông đốt cháy hỗn hợp không khí-nhiên liệu khi tiếp xúc với các bộ phận chuyển động. Điểm khác biệt quan trọng để phân biệt động cơ diesel là nó không có hệ thống đánh lửa bằng tia lửa điện. So với động cơ xăng có cùng mã lực, động cơ diesel nặng hơn và đắt hơn, nhưng nó có tuổi thọ cao hơn và hoạt động với chi phí thấp hơn trên mỗi mã lực-giờ vì nó đốt ít nhiên liệu hơn.
Động cơ khí có nhiều điểm chung với động cơ xăng; trên thực tế, trong một số trường hợp, sự khác biệt của chúng là rất nhỏ. Về mặt cấu trúc, sự khác biệt chủ yếu nằm ở việc thay thế van trộn khí (gas-mixing valve) cho bộ chế hòa khí. Cấu hình xi-lanh và pít-tông là giống nhau. Nói chung, khí có đặc tính chống kích nổ tốt hơn xăng, cho phép tỷ số nén cao hơn một chút mà không bị kích nổ hoặc các vấn đề cháy khác.
Từ quan điểm ứng dụng, động cơ khí đốt khí tự nhiên, khí sản xuất hoặc khí phụ phẩm công nghiệp chủ yếu bị giới hạn trong việc sử dụng cho nhà máy điện cố định vì nó phải duy trì kết nối với đường ống dẫn khí. Tuy nhiên, nếu nhiên liệu là khí dầu mỏ hóa lỏng (liquefied petroleum gas), đôi khi được gọi là khí đóng chai, các bình chứa khí có thể được mang theo trong xe, dẫn đến tính linh hoạt cao trong các ứng dụng. Trở ngại hiện nay là các cơ sở không có sẵn để bổ sung nguồn cung cấp khí.
Lịch sử phát triển động cơ xăng
Trong khi những nỗ lực chế tạo động cơ nhiệt đã được thực hiện từ thời cổ đại, động cơ hơi nước (steam engine) của thế kỷ 18 là loại động cơ thành công đầu tiên. Động cơ đốt trong, xuất hiện vào thế kỷ 19 như một sự cải tiến so với động cơ hơi nước cho nhiều ứng dụng, không thể được quy cho bất kỳ một nhà phát minh duy nhất nào. Pít-tông, được cho là có từ năm 150 trước Công nguyên, đã được các thợ kim loại sử dụng trong máy bơm để thổi khí. Hệ thống pít-tông và xi-lanh là cơ sở cho động cơ hơi nước, đưa bộ phận này lên một mức độ hiệu quả cao. Tuy nhiên, động cơ hơi nước có hiệu suất nhiệt thấp, trọng lượng và kích thước lớn, và vận hành bất tiện, tất cả đều chủ yếu là do nhiên liệu phải được đốt trong một lò riêng biệt với động cơ. Rõ ràng là cần có một bộ nguồn tự cấp.
Ngay từ thế kỷ 17, một số nhà thực nghiệm đã lần đầu tiên thử sử dụng các sản phẩm khí nóng để vận hành máy bơm. Đến năm 1820, một động cơ đã được chế tạo ở Anh, trong đó hỗn hợp hydro-không khí được đốt cháy trong một buồng. Sau đó, buồng được làm mát để tạo ra chân không tác động lên pít-tông. Việc bán các động cơ khí như vậy bắt đầu vào năm 1823. Chúng nặng nề và thô sơ nhưng chứa nhiều yếu tố thiết yếu của các thiết bị sau này, thành công hơn. Năm 1824, kỹ sư người Pháp Sadi Carnot đã xuất bản cuốn sách nhỏ kinh điển “Những suy ngẫm về động lực của nhiệt”, phác thảo lý thuyết cơ bản về động cơ đốt trong. Trong vài thập kỷ tiếp theo, các nhà phát minh và kỹ sư đã chế tạo các động cơ sử dụng áp suất được tạo ra bởi quá trình đốt cháy nhiên liệu thay vì chân không và các động cơ trong đó nhiên liệu được nén trước khi đốt. Tuy nhiên, không ai trong số họ thành công trong việc phát triển một hệ thống hoạt động. Cuối cùng, vào năm 1860, Étienne Lenoir của Pháp đã đưa ra thị trường một động cơ hoạt động bằng khí đốt và cung cấp dịch vụ tương đối thỏa đáng. Động cơ Lenoir về cơ bản là một động cơ hơi nước tác động kép (double-acting) được chuyển đổi với các van trượt (slide valves) để nạp khí và không khí và để xả các sản phẩm thải. Mặc dù động cơ Lenoir tạo ra ít công suất và chỉ sử dụng khoảng 4% năng lượng trong nhiên liệu, hàng trăm thiết bị này đã được sử dụng ở Pháp và Anh trong vòng 5 năm. Chúng được sử dụng để cung cấp năng lượng cho máy bơm nước và máy in và để hoàn thành một số công việc khác chỉ yêu cầu công suất đầu ra hạn chế.
Một tiến bộ lý thuyết lớn đã xảy ra với việc xuất bản vào năm 1862 một mô tả về chu trình hoạt động lý tưởng của động cơ đốt trong. Tác giả, kỹ sư người Pháp Alphonse Beau de Rochas, đã đưa ra các điều kiện sau đây là cần thiết để đạt hiệu suất tối ưu: thể tích xi-lanh tối đa với bề mặt làm mát tối thiểu, tốc độ giãn nở tối đa, tỷ lệ giãn nở tối đa và áp suất của hỗn hợp được đốt cháy tối đa. Ông mô tả trình tự hoạt động cần thiết là (1) hút trong toàn bộ hành trình đi ra của pít-tông, (2) nén trong hành trình đi vào tiếp theo, (3) đốt cháy hỗn hợp ở điểm chết trên (dead centre) và giãn nở trong hành trình đi ra tiếp theo (hành trình sinh công), và (4) đẩy khí đã cháy ra ngoài trong hành trình đi vào tiếp theo. Do đó, động cơ mà Beau de Rochas mô tả có chu trình bốn kỳ (four-stroke cycle), trái ngược với chu trình hai kỳ (nạp-đánh lửa và nổ-xả) của động cơ Lenoir. Beau de Rochas chưa bao giờ chế tạo động cơ của mình, và không có động cơ bốn kỳ nào xuất hiện trong hơn một thập kỷ. Cuối cùng, vào năm 1876, kỹ sư người Đức Nikolaus A. Otto đã chế tạo một động cơ đốt trong dựa trên nguyên tắc của Beau de Rochas. (Công ty của Otto, Otto và Langen, đã sản xuất và đưa ra thị trường một động cơ hai kỳ cải tiến vài năm trước đó.) Động cơ bốn kỳ Otto đã thành công ngay lập tức. Mặc dù có trọng lượng lớn và hiệu suất kém, gần 50.000 động cơ với tổng công suất khoảng 200.000 mã lực đã được bán trong 17 năm, tiếp theo là sự phát triển nhanh chóng của nhiều loại động cơ cùng loại. Việc sản xuất động cơ Otto tại Hoa Kỳ bắt đầu vào năm 1878, sau khi Otto được cấp bằng sáng chế Hoa Kỳ vào năm 1877.
Tám năm sau, Gottlieb Daimler và Wilhelm Maybach, những cộng sự cũ của Otto, đã phát triển động cơ bốn kỳ tốc độ cao thành công đầu tiên và phát minh ra bộ chế hòa khí (carburetor) giúp có thể sử dụng xăng làm nhiên liệu. Họ đã sử dụng động cơ của mình để cung cấp năng lượng cho một chiếc xe đạp (có lẽ là chiếc xe máy đầu tiên trên thế giới) và sau đó là một chiếc xe bốn bánh. Cùng thời điểm đó, một kỹ sư cơ khí người Đức khác, Karl Benz, đã chế tạo một động cơ xăng một xi-lanh để cung cấp năng lượng cho chiếc xe thường được coi là ô tô thực tế đầu tiên. Các động cơ do Daimler, Maybach và Benz chế tạo về cơ bản giống với động cơ xăng cơ bản ngày nay. Để biết thông tin về các cải tiến và tiến bộ sau này, hãy xem ô tô (automobile).
- Gasoline engine – Động cơ xăng